What’s the steps of Produce PVC panel ?
Producing PVC ceiling panels typically involves a series of manufacturing processes that transform raw materials into finished panels. Here’s a general overview of the steps involved in PVC ceiling panel production:
- Raw Material Preparation: The first step is to prepare the raw materials required for PVC ceiling panel production. This typically involves:
- PVC Resin: The primary ingredient, which provides the structural integrity of the panels.
- Plasticizers: To increase flexibility and workability of the PVC resin.
- Stabilizers: To prevent degradation of the PVC resin during processing and use.
- Fillers: To improve mechanical properties and reduce production costs.
- Pigments and Colorants: To add color and aesthetic appeal to the panels.
- Mixing: The raw materials are mixed together in precise proportions in a mixer to form a homogeneous mixture. This mixture will serve as the feedstock for the extrusion process.
- Extrusion: The mixed PVC material is fed into an extruder, where it is heated and pressurized to form a molten mass. The molten PVC is forced through a die, which shapes the material into continuous sheets with the desired thickness and width. These sheets will become the PVC ceiling panels.
- Cooling and Calibration: The extruded PVC sheets pass through a series of cooling rollers or a water bath to solidify and cool the material. At the same time, calibration equipment helps to shape the panels to the desired dimensions and thickness.
- Surface Treatment: After calibration, the PVC panels may undergo surface treatment processes to achieve specific textures, patterns, or finishes. This can include embossing, printing, or laminating processes to enhance the appearance and functionality of the panels.
- Cutting and Sizing: Once the surface treatment is complete, the PVC panels are cut to the desired length using cutting machinery. The panels may also be trimmed to ensure uniformity and precision in size.
- Quality Control: Throughout the production process, quality control measures are implemented to ensure that the PVC ceiling panels meet the required specifications and standards. This may involve inspecting the panels for defects, measuring dimensional accuracy, and testing mechanical properties.
- Packaging and Storage: The finished PVC ceiling panels are packaged for storage, transportation, and distribution. They may be wrapped in protective film, stacked on pallets, and stored in warehouses before being shipped to customers.
By following these steps, manufacturers can produce high-quality PVC ceiling panels suitable for a variety of residential, commercial, and industrial applications. Each step in the production process requires careful attention to detail to ensure the final product meets the desired standards for performance, appearance, and durability.
What raw materials used in produce the pvc panel ?
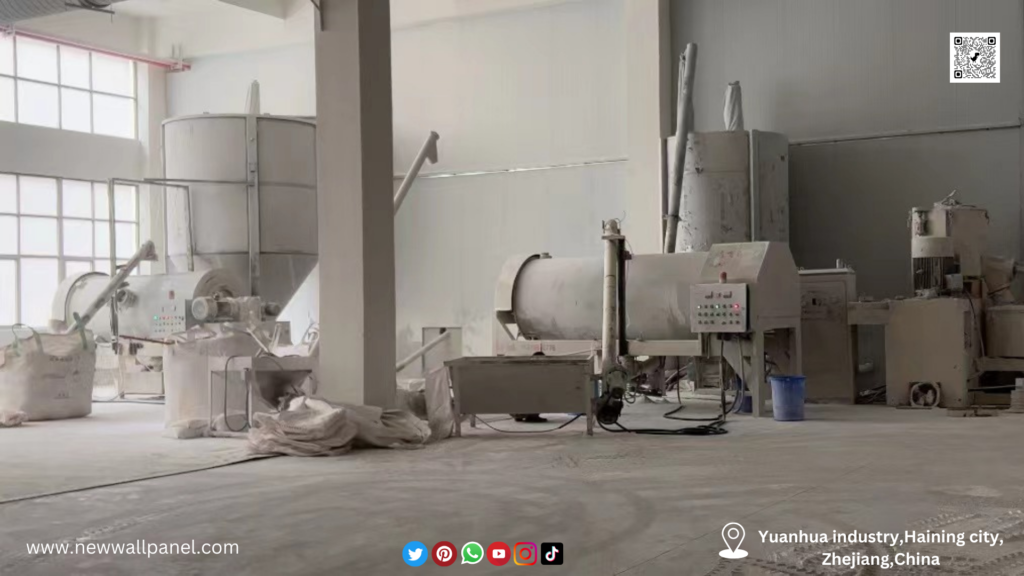
The production of PVC (polyvinyl chloride) panels typically involves several raw materials, each serving a specific purpose in the manufacturing process. The primary raw materials used in the production of PVC panels include:
- PVC Resin: PVC resin is the primary ingredient in PVC panels. It is a synthetic polymer derived from vinyl chloride monomers through polymerization. PVC resin provides the structural integrity and rigidity to the panels.
- Plasticizers: Plasticizers are added to PVC resin to increase flexibility and workability. They help to soften the PVC resin and make it more pliable during the manufacturing process, allowing it to be shaped into panels of various sizes and thicknesses. Common plasticizers used in PVC panel production include phthalates and adipates.
- Stabilizers: Stabilizers are additives that help to prevent PVC panels from degrading when exposed to heat, light, or other environmental factors. They stabilize the PVC resin and improve its resistance to degradation, extending the lifespan of the panels. Common stabilizers used in PVC panel production include lead-based compounds, calcium-zinc stabilizers, and organotin compounds.
- Fillers: Fillers are inert materials added to PVC panels to improve their mechanical properties, reduce production costs, and enhance dimensional stability. Common fillers used in PVC panel production include calcium carbonate, talc, and kaolin. Fillers also help to reduce the overall weight of the panels and improve their fire resistance.
- Pigments and Colorants: Pigments and colorants are added to PVC panels to provide color and aesthetic appeal. They can be used to create panels in a wide range of colors and patterns to suit different design preferences and applications.
- Processing Aids: Processing aids are additives that help to improve the processing and handling characteristics of PVC resin during manufacturing. They may include lubricants, dispersants, and anti-static agents, which facilitate the extrusion, molding, or foaming processes used to produce PVC panels.
- Foaming Agents (for foam panels): If producing foam PVC panels, foaming agents are added to the PVC resin to create a cellular structure within the panels, resulting in lightweight, insulating, and buoyant properties.
These raw materials are carefully selected and combined in specific formulations to meet the desired performance, appearance, and regulatory requirements for PVC panels. The precise composition of PVC panel formulations may vary depending on factors such as application, manufacturer specifications, and regional regulations.
- Related articals:
What-is-pvc-panel-the-most-comprehensive-pvc-panel-introduction
What kind of machines can produce PVC panel ?
The production of PVC (polyvinyl chloride) panels typically involves several types of machinery and equipment designed to carry out various processes in the manufacturing process. Here are some of the key machines used in the production of PVC panels:
- Mixer: Mixers are used to blend the raw materials required for PVC panel production. They combine PVC resin, plasticizers, stabilizers, fillers, pigments, and other additives in precise proportions to form a homogeneous mixture.
- Extruder: Extruders are crucial machines in PVC panel production. They heat and pressurize the PVC mixture, forcing it through a die to produce continuous sheets or profiles with the desired shape and dimensions. Single-screw or twin-screw extruders may be used depending on the complexity of the panel design and production requirements.
- Calibration Table: Calibration tables are used to cool and shape the extruded PVC panels to the desired thickness and dimensions. They often feature water-cooled rollers or vacuum chambers to control the cooling process and ensure uniform panel thickness.
- Embossing Machine: Embossing machines apply texture or patterns to the surface of PVC panels to enhance their aesthetic appeal. They use heated rollers or molds to imprint designs onto the panels during the production process.
- Cutting Machine: Cutting machines are used to trim and cut the extruded PVC panels to the required length and shape. They may employ saw blades, guillotine cutters, or other cutting mechanisms to achieve accurate cuts with clean edges.
- Surface Treatment Equipment: Surface treatment equipment may include machines for applying surface coatings, laminates, or protective films to PVC panels. These treatments can enhance the durability, appearance, and performance of the panels for specific applications.
- Packaging Equipment: Packaging equipment is used to package the finished PVC panels for storage, transportation, and distribution. This may include machines for wrapping panels in protective film, stacking panels on pallets, and shrink-wrapping or bundling panels for shipping.
- Quality Control Equipment: Quality control equipment, such as thickness gauges, color spectrophotometers, and surface inspection systems, is used to ensure that PVC panels meet the required specifications and quality standards throughout the production process.
These are some of the main types of machines used in the production of PVC panels. The specific machinery and equipment used may vary depending on factors such as the size and complexity of the panels, production volume, and technological advancements in PVC panel manufacturing processes.
How big area request if open a PVC PANEL factory ?
The size of the area required to open a PVC panel factory can vary significantly depending on several factors, including the scale of production, the variety of products manufactured, the layout of the production process, and the availability of space for expansion. However, I can provide a general guideline based on typical factory sizes for PVC panel production.
For a small to medium-sized PVC panel manufacturing facility, you would likely need a minimum area of around 5,000 to 10,000 square feet (465 to 930 square meters). This space would accommodate the production equipment, storage areas for raw materials and finished products, office space, quality control areas, and other necessary facilities.
For larger-scale operations or factories producing a wide range of PVC panel products, you may require a significantly larger area, ranging from 20,000 to 50,000 square feet (1,860 to 4,645 square meters) or more. This would allow for additional production lines, increased storage capacity, and potentially larger office and administrative areas.
It’s also important to consider factors such as ceiling height, access to utilities (electricity, water, gas), ventilation and environmental control systems (especially if producing foamed PVC panels), and compliance with local building codes and regulations.
Additionally, it’s advisable to plan for future expansion when determining the size of the factory space. As your business grows and production capacity increases, you may need to expand your facilities to meet demand and accommodate new equipment and processes.
Overall, the size of the area required to open a PVC panel factory can vary based on your specific production needs, business goals, and available resources. It’s essential to conduct a thorough feasibility study and consult with experts in PVC panel manufacturing to determine the most suitable facility size for your operation.
Who is the biggest PVC panel export country ?
As i known,China is one of the largest exporters of PVC panels in the world. China’s manufacturing industry, including PVC panel production, has experienced significant growth over the past few decades, driven by factors such as large-scale production capabilities, relatively low labor costs, and a strong export-oriented economy.
Other countries that are significant exporters of PVC panels include India, Germany, the United States, and the United Arab Emirates. These countries also have well-established manufacturing industries and export networks, allowing them to supply PVC panels to markets around the world.
It’s important to note that the exact ranking of the largest PVC panel export countries may vary over time, depending on factors such as changes in production capacity, economic conditions, trade policies, and global demand for PVC panels. Additionally, specific market dynamics and trade relationships may influence the export volumes of individual countries in any given year.
For the most up-to-date information on PVC panel export statistics and trends, it’s advisable to consult reliable sources such as industry reports, trade databases, and government publications.
Which areas or cities of china producing pvc wall panels ?
Several areas and cities in China are known for producing PVC panels due to their concentration of manufacturing facilities and industrial infrastructure. Some of the key regions and cities include:
- Guangdong Province: Guangdong is one of the major manufacturing hubs in China and is home to numerous PVC panel production facilities. Cities such as Foshan, Dongguan, and Guangzhou have a significant presence of PVC panel manufacturers.
- Zhejiang Province: Zhejiang Province is another important region for PVC panel production. Cities like Hangzhou(major is haining city yuanhua town), Ningbo, and Wenzhou are known for their manufacturing clusters, including those producing PVC panels.
- Shandong Province: Shandong Province is a major industrial base in China and has several cities involved in PVC panel manufacturing. Qingdao, Jinan, and Weifang are among the cities in Shandong known for PVC panel production.
- Jiangsu Province: Jiangsu Province hosts a variety of industries, including PVC panel manufacturing. Cities like Suzhou, Nanjing, and Wuxi have a presence of PVC panel producers.
- Shanghai: As one of China’s most developed and industrialized cities, Shanghai also has PVC panel manufacturing facilities catering to domestic and international markets.
- Hubei Province: Hubei Province, particularly the city of Wuhan, has a growing presence in PVC panel production, serving both domestic and export markets.
- Henan Province: Henan Province, with cities like Zhengzhou and Luoyang, is emerging as a location for PVC panel manufacturing, benefiting from its central location and access to transportation networks.
These regions and cities in China benefit from various factors such as infrastructure, skilled labor, access to raw materials, and transportation networks, which contribute to their prominence in PVC panel production. However, PVC panel manufacturing facilities can be found in other provinces and cities across China as well.
Haining is well-known as PVC panel manufacturer city?
Yes, Haining, located in Zhejiang Province, China, is indeed well-known as a significant PVC panel manufacturing city. Haining has a long history of industrial development and is particularly renowned for its production of various building materials, including PVC panels.
The city’s reputation as a PVC panel manufacturing hub stems from several factors:
- Industry Clusters: Haining is home to numerous PVC panel manufacturers, creating an industry cluster that benefits from economies of scale, access to skilled labor, and shared infrastructure.
- Market Presence: PVC panel manufacturers in Haining have established a strong presence in both domestic and international markets, supplying a wide range of PVC panel products for construction, interior decoration, and other applications.
- Technological Expertise: Manufacturers in Haining have developed expertise in PVC panel production techniques, including extrusion, embossing, and surface treatment, allowing them to produce high-quality panels with diverse designs and specifications.
- Supply Chain Integration: Haining benefits from a well-developed supply chain ecosystem, with access to raw materials, components, and machinery required for PVC panel production. This facilitates efficient manufacturing processes and reduces production costs.
- Export-Oriented Economy: Haining’s PVC panel manufacturers are often export-oriented, capitalizing on the city’s strategic location near major ports and transportation networks for international trade.
Overall, Haining’s reputation as a PVC panel manufacturing city is well-established, and it continues to play a significant role in China’s PVC panel industry, contributing to the city’s economic growth and industrial development.