Exploring the Benefits and Applications of UV Board PVC Panels
What is UV board?
UV board, also known as UV coated board or UV-cured board, refers to a type of engineered wood product that has been coated with a layer of ultraviolet (UV) cured finish. This finish is applied to the surface of the board and then cured or hardened using UV light. The UV curing process creates a durable and protective coating that enhances the appearance and performance of the board.
UV board is typically made from a substrate material such as medium-density fiberboard (MDF), particleboard, or plywood. These substrates are engineered wood products composed of wood fibers, particles, or veneers bonded together with resin or adhesive under heat and pressure.
Once the substrate is manufactured, it undergoes a finishing process where a layer of UV-cured coating is applied to the surface. This coating may consist of acrylic, polyester, polyurethane, or other types of resin, depending on the desired properties and applications of the UV board.
The UV coating is applied to the board using a roller, spray gun, or other application method, and then exposed to UV light for curing. The UV light activates photoinitiators in the coating, causing it to polymerize and harden rapidly, forming a strong and durable protective layer.
UV board offers several advantages over traditional finishes such as solvent-based or water-based coatings:
- Durability: The UV-cured finish provides excellent resistance to scratches, abrasions, chemicals, and fading, resulting in a durable and long-lasting surface.
- Fast Curing Time: UV curing is a rapid process, allowing for quick production cycles and increased productivity compared to other curing methods.
- Environmental Benefits: UV coatings are typically solvent-free and emit low levels of volatile organic compounds (VOCs), making them environmentally friendly and compliant with regulations on air quality and emissions.
- Enhanced Appearance: UV-cured coatings can be formulated to provide a high-gloss, matte, or satin finish, as well as a wide range of colors and effects, enhancing the aesthetic appeal of the board.
- Ease of Maintenance: UV-coated surfaces are easy to clean and maintain, requiring minimal effort to remove dirt, dust, and stains.
UV board is commonly used in a variety of applications, including furniture manufacturing, cabinetry, interior decoration, architectural millwork, signage, and displays. Its versatility, durability, and aesthetic appeal make it a popular choice for modern design and construction projects.
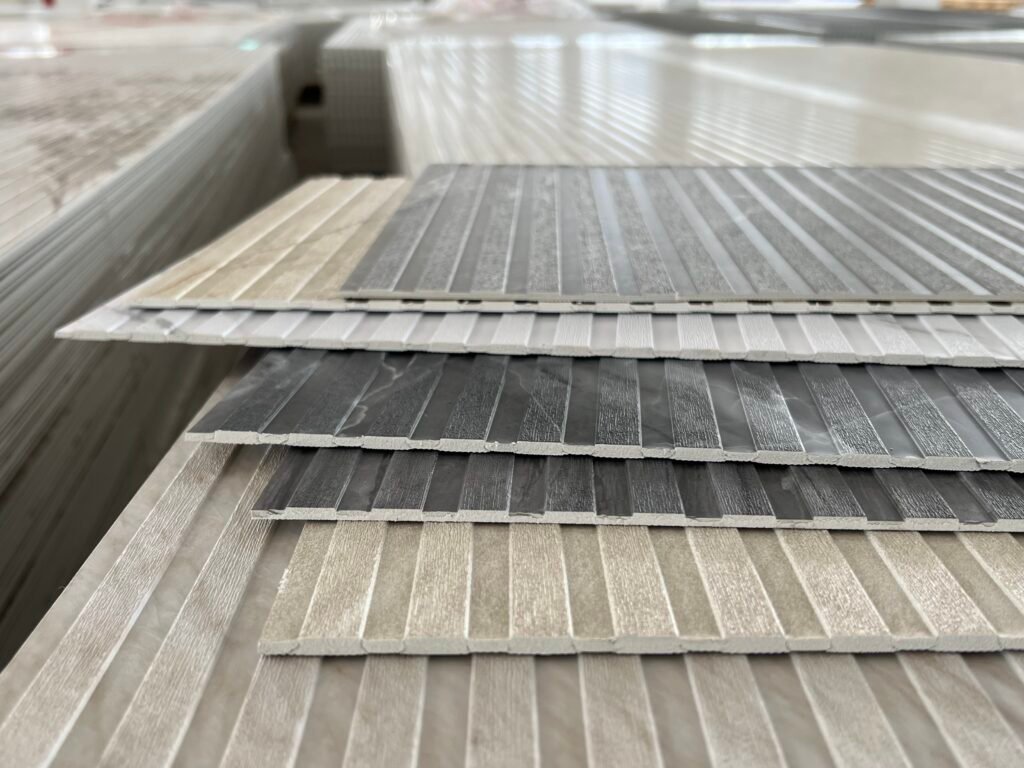
UV board also called UV panel ?
Yes, UV board is also commonly referred to as UV panel. Both terms are used interchangeably to describe engineered wood products that have been coated with a layer of ultraviolet (UV) cured finish. This UV coating provides durability, scratch resistance, and aesthetic enhancements to the surface of the board.
UV boards or UV panels are widely used in various industries, including furniture manufacturing, interior decoration, architectural millwork, signage, and displays. They offer versatility in design, as well as durability and ease of maintenance, making them a popular choice for modern design and construction projects.
Whether called UV board or UV panel, these engineered wood products undergo a specialized UV curing process to create a protective coating that enhances the appearance and performance of the board. They are available in a range of colors, finishes, and textures to suit different applications and design preferences.
UV board size
The size of UV boards can vary depending on the manufacturer and the specific application. However, UV boards are commonly available in standard sizes to accommodate various needs in the construction, furniture, and interior design industries. Here are some typical dimensions for UV boards:
- Thickness: UV boards typically come in various thicknesses, ranging from as thin as 2mm to as thick as 25mm or more. The choice of thickness depends on the intended use of the board, with thicker boards often used for structural purposes or heavy-duty applications.
- Width: UV boards are available in different widths, commonly ranging from 1220mm (4 feet) to 2440mm (8 feet). The width of the board may vary based on manufacturing capabilities and customer requirements.
- Length: The length of UV boards can also vary, with standard lengths typically ranging from 2440mm (8 feet) to 3050mm (10 feet) or longer. Longer lengths may be available for certain applications or custom orders.
- Custom Sizes: In addition to standard sizes, UV boards can also be custom-cut or fabricated to meet specific project requirements. Custom sizes may be available upon request from manufacturers or suppliers, allowing for greater flexibility and customization in design and construction projects.
It’s important to note that while standard sizes are readily available, the availability of specific dimensions may vary depending on factors such as the manufacturer’s production capabilities, stock levels, and regional market preferences. Additionally, some manufacturers may offer pre-cut or pre-fabricated UV boards in standard sizes for convenience and ease of use in various applications.
Does UV board expensive ?
The cost of UV-coated boards can vary depending on several factors, including the type of substrate material, the quality of the UV coating, the manufacturer, and the supplier. Generally, UV-coated boards may be considered more expensive compared to some other types of engineered wood products or surface finishes. However, the cost of UV boards can vary depending on the following factors:
- Substrate Material: UV-coated boards can be made from various substrate materials such as medium-density fiberboard (MDF), particleboard, plywood, or even PVC (polyvinyl chloride). The cost of the substrate material can affect the overall price of the UV board.
- UV Coating Quality: The quality of the UV coating applied to the board can vary, with higher-quality coatings providing better durability, scratch resistance, and UV protection. UV boards with premium-grade coatings may command a higher price due to their superior performance and longevity.
- Manufacturer and Brand: Different manufacturers and brands may offer UV-coated boards at varying price points based on factors such as reputation, quality standards, and production processes. Established brands known for their quality and reliability may charge higher prices for their UV boards.
- Size and Thickness: The size and thickness of the UV-coated boards can also impact the cost, with larger or thicker boards typically costing more than smaller or thinner ones. Custom sizes or thicknesses may also incur additional charges.
- Customization and Design: UV-coated boards with custom colors, patterns, textures, or finishes may be more expensive than standard options due to the additional manufacturing processes and customization involved.
- Quantity and Ordering Volume: Bulk purchases or larger quantities of UV-coated boards may be eligible for volume discounts or wholesale pricing, helping to reduce the overall cost per unit.
Ultimately, while UV-coated boards may be considered more expensive compared to some alternatives, they offer several benefits such as enhanced durability, scratch resistance, and aesthetic appeal, which may justify the investment for certain applications or projects. It’s essential to consider factors such as quality, performance, and longevity when evaluating the overall value of UV-coated boards relative to their cost.
Matte VS. Glossy UV board(panel)
Matte and glossy UV boards are two common finishes applied to UV-coated boards, each offering distinct aesthetic and functional characteristics. Here’s a comparison between matte and glossy UV boards:
Matte UV Board:
- Appearance: Matte UV boards have a flat or non-reflective finish, providing a subtle and understated appearance. They offer a soft, velvety texture that diffuses light rather than reflecting it.
- Aesthetic: Matte finishes are often preferred for their elegant and sophisticated look, adding a touch of understated luxury to interior spaces.
- Durability: Matte UV boards are less prone to showing fingerprints, smudges, or scratches compared to glossy finishes, making them ideal for high-traffic areas or applications where surface imperfections are a concern.
- Maintenance: Matte UV boards are relatively easy to maintain, requiring minimal effort to clean and maintain their appearance. They are less prone to visible marks or streaks from cleaning compared to glossy finishes.
- Applications: Matte UV boards are suitable for a wide range of applications, including furniture manufacturing, cabinetry, interior decoration, architectural millwork, and signage, where a subtle and refined aesthetic is desired.
Glossy UV Board:
- Appearance: Glossy UV boards have a high-shine, reflective finish that creates a sleek and polished look. They offer a mirror-like surface that reflects light, resulting in vibrant colors and enhanced visual impact.
- Aesthetic: Glossy finishes are often chosen for their modern and contemporary appeal, adding a sense of luxury and sophistication to interior spaces.
- Durability: Glossy UV boards may show fingerprints, smudges, or scratches more readily than matte finishes due to their reflective surface. However, they can be coated with additional protective layers to enhance durability and resistance to wear and tear.
- Maintenance: Glossy UV boards require regular cleaning and maintenance to preserve their glossy appearance and minimize visible marks or streaks. Specialized cleaning products and techniques may be needed to achieve optimal results without causing damage to the surface.
- Applications: Glossy UV boards are commonly used in applications where visual impact and aesthetic appeal are paramount, such as high-end furniture, luxury interiors, decorative accents, and architectural features.
Ultimately, the choice between matte and glossy UV boards depends on personal preferences, design considerations, and the specific requirements of the project. Both finishes offer unique benefits and can be used to achieve different design effects, allowing for versatile and customizable solutions in interior design and construction.
Does UV board waterproof and anti-fire?
UV-coated boards can offer varying degrees of water resistance and fire resistance depending on the specific materials used in their construction and the properties of the UV coating applied to the surface. Here’s a breakdown of their waterproof and fire-resistant characteristics:
- Water Resistance:
- UV-Coated Surface: The UV coating applied to the surface of UV boards can provide some level of water resistance, protecting the underlying substrate from moisture infiltration. However, the degree of water resistance may vary depending on the quality and composition of the UV coating.
- Substrate Material: The substrate material used in UV boards can also impact their water resistance. For example, UV boards made from moisture-resistant materials such as PVC (polyvinyl chloride), fiberglass-reinforced panels (FRP), or waterproof MDF (medium-density fiberboard) may offer better water resistance compared to standard MDF or particleboard.
- Installation and Sealing: Proper installation techniques, including sealing joints, edges, and penetrations, can further enhance the water resistance of UV boards, particularly in wet or high-moisture environments such as bathrooms or kitchens.
- Fire Resistance:
- UV-Coated Surface: While the UV coating itself may not provide inherent fire resistance, UV boards can be manufactured with fire-retardant additives or treated with fire-resistant coatings to improve their fire resistance properties.
- Substrate Material: The substrate material used in UV boards can influence their fire resistance. For example, some UV boards are made from fire-rated MDF or particleboard, which are engineered to meet specific fire safety standards and regulations.
- Fire Rating: UV boards may be tested and certified to meet certain fire safety standards, such as Class A, B, or C fire ratings, indicating their performance in fire testing scenarios. It’s essential to verify the fire rating of UV boards and ensure compliance with local building codes and regulations.
In summary, while UV-coated boards may offer some level of water resistance and fire resistance, their specific characteristics can vary depending on factors such as substrate material, UV coating composition, and manufacturing processes. It’s crucial to select UV boards with the appropriate properties for the intended application and ensure proper installation and compliance with relevant safety standards for optimal performance.
UV board can installed in the washroom and kitchen area ?
Yes, UV-coated boards can be installed in the washroom, but it’s essential to choose the appropriate type of board and ensure proper installation to withstand the humid and wet conditions commonly found in bathrooms. Here are some considerations for installing UV-coated boards in the washroom:
- Moisture Resistance: Select UV-coated boards that are specifically designed for moisture-prone areas such as bathrooms. These boards are typically made from materials that are resistant to moisture and humidity, such as PVC (polyvinyl chloride) or moisture-resistant MDF (medium-density fiberboard).
- Waterproofing: Ensure that the installation is properly waterproofed to prevent water infiltration behind the boards. This may involve applying a waterproof membrane or sealant to the substrate before installing the UV-coated boards.
- Sealing Joints and Edges: Seal the joints and edges of the UV-coated boards with a waterproof sealant or caulk to prevent water from seeping between the panels and causing damage to the substrate.
- Proper Ventilation: Ensure adequate ventilation in the bathroom to minimize moisture buildup and condensation, which can lead to mold and mildew growth on the surface of the UV-coated boards.
- Maintenance: Regularly clean and maintain the UV-coated boards to prevent the buildup of soap scum, grime, and other residues. Use mild detergent and water to clean the surface, avoiding harsh chemicals or abrasive cleaners that may damage the UV coating.
- Avoid Direct Water Contact: While UV-coated boards are water-resistant, prolonged exposure to standing water or direct water contact should be avoided. Wipe up any spills or splashes promptly to prevent water damage to the boards.
- Considerations for Flooring: If installing UV-coated boards on the bathroom floor, choose boards specifically designed for flooring applications and ensure proper waterproofing and sealing to prevent water damage and ensure safety.
By following these guidelines and selecting the appropriate UV-coated boards for your bathroom, you can enjoy the aesthetic benefits of UV-coated boards while ensuring durability and longevity in a moisture-prone environment.
UV panel easy to install ?
Yes, UV panels are generally considered to be easy to install, especially when compared to other types of wall cladding or surface finishes. Here are several reasons why UV panels are often considered straightforward to install:
- Lightweight: UV panels are typically lightweight, making them easier to handle and maneuver during the installation process. This can reduce the need for heavy lifting equipment and simplify installation tasks.
- Modular Design: Many UV panels are designed to interlock or fit together seamlessly, creating a modular system that simplifies installation and ensures uniformity in the finished surface.
- Versatile Installation Options: UV panels can be installed using various methods, including adhesive bonding, mechanical fastening, or tongue-and-groove interlocking systems. This versatility allows installers to choose the most suitable method for the specific application and substrate material.
- No Specialized Tools Required: In many cases, installing UV panels does not require specialized tools or equipment beyond basic carpentry tools such as a saw, drill, level, and measuring tape. This makes the installation process accessible to DIY enthusiasts and professional installers alike.
- Pre-Finished Surface: UV panels come with a pre-finished surface, eliminating the need for additional finishing treatments such as painting or staining. This can save time and labor during installation and reduce the overall project timeline.
- Minimal Surface Preparation: Unlike some other wall cladding materials that require extensive surface preparation, UV panels can often be installed directly onto clean, dry, and smooth substrates with minimal preparation required.
- Interchangeable Panels: In the event of damage or wear, individual UV panels can be easily replaced without the need for extensive demolition or reconstruction, providing flexibility and ease of maintenance over time.
While UV panels are generally considered easy to install, it’s essential to follow manufacturer guidelines and recommendations for proper installation techniques to ensure optimal results. Additionally, hiring a professional installer may be advisable for more complex installations or larger projects to ensure accuracy, efficiency, and safety.
Where is the uv panel factory?
The location of UV panel factories can vary widely, as there are manufacturing facilities situated in different regions and countries around the world. The production of UV panels is not restricted to a specific geographical area, and you can find factories in various countries based on factors such as cost, quality, and market demand.
Some regions known for manufacturing and exporting building materials, including UV panels, include:
China is a major manufacturing hub for various building materials, including UV panels. Many factories in China produce a wide range of UV-coated boards for domestic and international markets. Haining city is one the biggest manufacturer areas. www.newwallpanel.com